Case study: Submarine and Floating Hose Change out
In 2018 Marsol was contracted to undertake the complete change out of subsea and floating hoses originally installed by an EPC contractor 6 years previously. On this particular system, hose sections had never previously been tested individually.
The Problem: Complete Hose Change out
The client’s SPM floating and subsea hoses were reaching the end of their predicted life expectancy and needed to be replaced. In order to minimize disruption to operations, this process had to be undertaken as quickly and efficiently as possible.
Some risks that had to be considered:
- Damaging the new hoses during handling and deployment
- Towing the floating hose and crossing shipping lanes
- Inadequate string assembly if performed at sea
The removal of old- and installation of new hoses on the buoy had to be undertaken as quickly as possible. Removed hoses needed to be inspected and tested to investigate any root causes of failure/wear that may contribute to increased long-term operational costs, and to determine their suitability for reuse
The Solution
Assemble the Marsol Hose Deployment Roller System at a suitable access site on the beach nearest the SPM. Load out hose sections and connect into a string in the dry. Tow the hose off the beach for a straight swap at the buoy offshore. Bring the old hose back to the beach for immediate recovery & disassembly.
The Process
This two-month project was tactically programmed to ensure the minimum viable product for the client, whereby large costs incurred by vessels and dive teams were only incurred for just over two weeks. The balance of the activities were executed by teams “on the beach” who made the materials ready for the offshore works.
To ensure that the SPM system was free from hydrocarbon product, and to avoid any spillage during the hose disconnection, the system was flushed with freshwater that was pumped from the floating hose end through the SPM, subsea hose and into the pipeline. This water-flush pushed the product down the fluid path into the pipeline towards the onshore storage tanks.
Subsea Hoses Change out
In this case, there was only one complete spare subsea hose-string, therefore a set of new subsea hoses had been purchased and delivered to the client ahead of the commencement of the project.
All subsea hoses were loaded on the Multicat Vessel in port, along with the tools and equipment required for the offshore works.
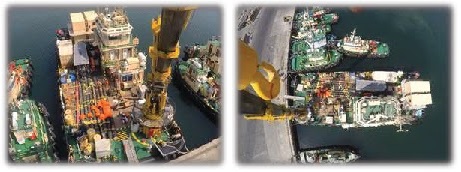
The subsea hose change out was performed on the Multicat deck successfully.
The hydraulic control umbilical was removed by the divers in order to allow work on the subsea hoses without damaging said umbilical. The first hose was then disconnected, removed, dismantled and discharged to a service vessel. The new hose was assembled and deployed into the water and installed under the buoy by the diving team.
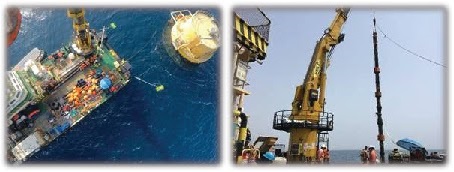
Similarly, the opposing hose was removed and replaced with the new string.
The removed hoses were sent ashore to be tested for residual life and serviceability.
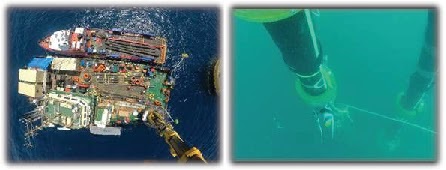
Floating Hose Change out
The second phase of this project was the floating hose change out which, although similar, required a different approach to that of the subsea hose change out.
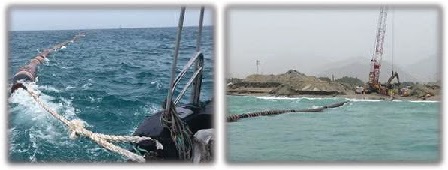
The Marsol onshore team commenced by loading and assembling the new floating hose on the Marsol Roller System. This modular hose deployment system increases efficiency but reduces risks and prevents the hose damage – usually incurred by ground contact and handling. The new Marine Breakaway Coupling (MBC) was assembled in the string and secured with special brackets to avoid activation while the hose string was towed to the SPM.
At the same time, the offshore team disconnected the old floating hose string and stored it, prior to removing it from the water – through the surf zone.
Back onshore, the newly assembled floating hose string was leak tested while on the Marsol Roller System, to ensure the integrity of the flange connections. The leak test was witnessed and signed-off by Class.
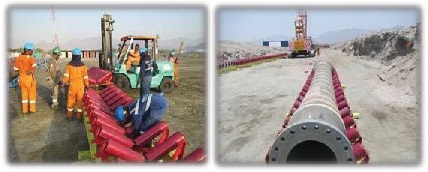
The newly assembled hose-string was then launched from the beach, towed to site and installed on the SPM.
Thereafter, the old floating hose was towed from the storage and recovered using the Marsol Roller System. The removed string was dismantled into individual hoses at the site and made ready for OCIMF testing.
SPM Pressure Test
To conclude the offshore works, a complete SPM system pressure test was performed by pumping water into the system from the floating hose, raising the pressure to the required level and holding the pressure for a certain number of hours. This test was undertaken in accordance with OCIMF and OEM guidelines, and was witnessed by CLASS.
OCIMF Testing and Storage of Removed Hoses
Following the recovery, all old hoses were cleaned, OCIMF tested and those suitable for reuse were stored in the storage containers.
Visual Testing
The result of the OCIMF and OEM visual inspection showed that some of the floating hoses failed the test and had to be retired.
The visual inspection also revealed that some of the subsea hoses had various superficial cuts and small areas of damage on the outer layer, however, those were allowed for further testing to ascertain suitability to be repaired and then held as spares.
Examples of superficially damaged hoses:
OCIMF Test Results
A number of hoses passed with reservations, while the recommendation for others was to be retired and not placed in storage for re-use
Test Result Findings
Based on the OCIMF testing, it was found that the hoses that passed the test could be kept as emergency spares up to the end of their shelf life (Estimated 10 years from the original date of manufacturing, as recommended by OEM and OCIMF guidelines).
Case Study Recommendations
It was Marsol’s recommendation that the client purchases additional spare hoses such that they can respond with replacement parts in case of a failure of any of the hose, or to change out short lifespan hoses like the FOB or Tanker Rail.
The recommendation was that the next OCIMF testing of the spare hoses to be done after two years to ensure that the emergency spare hoses are still suitable for service.
In this case it is planned to perform the hydrostatic burst test which would provide data that could be used to establish suitability for purpose, to gauge the extent of any damage and provide useful information to determine the service life and life extension of the hoses.
This information will be very important for new hose procurement planning.
In Closing
A SPM hose change out may be a routine procedure but is often overlooked as something that is not fully understood but done anyway ‘because it is required.’ This is a dangerous approach in the offshore industry because many protocols and procedures are no longer relevant, efficient or considered best practice. The method that Marsol describes in this article is the result of careful consideration of the particular site, the various design parameters of the assets and real-world conditions. The operation was executed safely and efficiently while exceeding the client expectations.
Let us help you achieve the same result. Get in touch to take charge of your next hose change out.
Project Report: OCIMF testing and Hose change out – what you see is not what you get.
When planning for SPM hose changeout project, it is paramount that the old hoses are tested, as this helps to determine wear patterns and root causes of hose decay or failure. Visual inspection does not tell all about the hoses’ condition and full OCIMF testing is recommended to properly understand the hose condition. Here’s what to expect when you are planning a hose changeout with OCIMF testing project.
Hose manufacturers typically recommend SPM hose changeout after 5 years (depending on certain parameters), but it may also be needed earlier due to unusual wear, damage or failure. Note that certain high-wear hoses have shorter lifespans. Catering for such events becomes easier when you have a solid SPM Hose Plan that favours longevity and sustainable reliability.
When it comes to SPM Hose testing, Marsol follows the regulations brought forth by the Oil Companies International Marine Forum (OCIMF), to ensure safe and environmentally friendly processes that are in accordance with the most modern standardised methods available.
Hose Changeout and Testing Activities and Schedule
First the team will divide the project into phases, depending on the scope. During a complete hose changeout project, the phases are likely to include:
• Phase 1: Testing of the new hoses (if they have been in prolonged storage or used before)
• Phase 2: Replacement of all hoses (Floating and Submarine)
• Phase 3: Testing of the removed hoses
The personnel involved in the phases would follow method statements specifically developed for the asset and its environmental conditions.
At Marsol these method statements are developed in line with the OCIMF Guidelines, International Standards (ISO, ISSGOT), OEM Manuals and industry best practice.
Hose Changeout Timeline
From start to finish, a project changing out a set of floating and subsea hoses can take 4 weeks. At Marsol, the proprietary Roller System for floating hose deployment is used. This system is specially designed to not only increase efficiency, but also minimise hose damage throughout the onshore part of the hose changeout procedure.
Using this system, the floating hose changeout part of two strings will see the SPM downtime reduced to just about a week, given streamlined conditions and excluding any unexpected events.
The team will begin with Mobilisation and Site Setup, to start OCIMF testing of spare hoses as soon as possible. Concurrently, assembly of the Roller System will start, and at the same time, offshore works at the SPM will begin in by disconnecting the old floating hoses and towing them to shore.
The submarine hose changeout and new floating hose installation will be performed next, ensuring that all SPM pressure tests are completed and Class witnessed.
Finally, the old hoses are OCIMF tested to identify potential decay trends or wear patterns that could result in a shortened lifespan. This will also identify hoses that can be reused as spares for times of emergency.
Hose Changeout General Considerations
- Hose testing should be performed according to the OCIMF Guidelines for the Handling, Storage, Inspection and Testing of Hoses on shore, 2nd Edition, 1995
- Both the submarine and floating hoses are to be tested according to the OEM specifications.
- Spare hoses to be used in the changeout should undergo testing according to OCIMF Guidelines before assembly and installation.
This includes:
- Visual inspection
- Hydrostatic pressure test
- Vacuum test
- Electrical test
- All the ancillary materials (gaskets, nuts and bolts) to be used as part of the assembly, will have to be checked.
New SPM hoses that have been factory tested prior to installation do not need to be tested again, as long as the manufacturer has supplied you with testing certificates.
OCIMF Test Data Measuring and Recording
For long-term improvements in operational efficiency, it is important to record data obtained from your hose changeout and testing. This means that every hose tested must be documented, including a visual reference, pressure, vacuum tests and graphs combined with time and pressures.
Indicators of Concern during Hose Inspection
During inspection and OCIMF testing the following indicators should alert the inspector that the hose may be in an unsatisfactory state:
Visual Inspection:
• Excessive cover/floatation damage.
• Crushed or kinked hose wall.
• Local reduction in bore diameter
• Distinct circumferential “ribbing” (indicating fatigue or fabrication flaw).
• Mechanically damaged lining.
• Lining separation from rest of hose wall (delamination).
• Movement of end fitting nipple relative to flexible hose section.
• Bulges/blisters (other than air pockets or local delamination in cover).
• Excessive fitting corrosion.
• Excessive wear to lifting lugs.
Hydrostatic test
• External leakage
• External bulge / bursting appears
• Difficulty holding pressure if not due to equipment malfunction (suggests leak path into hose wall)
In-Situ Pressure test:
• Failure of holding pressure
• Twist Warning System (TWS) activation
• Leak detector activation
Conclusion
SPM hose changeouts, whether they are routine or an emergency, cause down time and loss of operational capacity which is of major concern to SPM operators. It is the aim of every operator to undertake the changeouts as quickly and efficiently as possible. Marsol has developed methodology and the Roller System for hose deployment which ensure maximum speed and efficiency of the changeout process. OCIMF testing of the old hoses after the changeout is critical to understanding the condition of the hoses and any causes of the reduction in their life expectancy. This information can be used to make operational decisions and ensure the root causes of the failures are addressed.