Outsourcing hose management : Is it a good idea?
Your marine hoses can make or break your offshore terminal. While many companies feel the need to keep hose maintenance in-house, others are choosing to focus on their core business by bringing in specialist partners to whom they entrust hose management and maintenance instead. Here’s what to consider when deciding whether or not outsourcing hose maintenance is for you.
Hose Lifecycle management
While one may think an in-house team may be more familiar with the terminal and its operating history, this is not always true as an in-house team may inevitably rotate staff and the knowledge built up over time is either lost or taken for granted.
Outsourcing hose management means that hose assessments are performed to establish an operating history. These records are kept and disseminated to all the appropriate staff at the outsourced partner company who acts as a whole. Such outsourced hose assessments include OCIMFtesting, destructive testing and OEM laboratory testing.
This data is compared against the basis of design and design criteria which hose specialists will always be well familiar with. Outsourced hose management should support installation, validated methodologies and installed subsea hose profiles. At MASROL we develop a Hose Management Plan encompassing optimal storage, inspections, maintenance and procurement tailor-made for each unique client terminal.
For objective validation and investigation of abnormal events, an outsourced hose management partner will assess the effects on design integrity and life.
Continuous hose assessment objectives:
- Reducing the risk of hose related incidents
- Contributing towards Warranty Extension from OEM & Alliance Partners
- Establishing possible points of failure and mitigation programs
- Cost Certainty
- Maximisation of operational usage of hoses to achieve optimum life
- Contributing to operational and cost efficiencies
- Reducing downtime and interruptions
Hose inventory management, storage and testing
Oil & Gas marine hoses, as the main artery for product transfer, constitute a significant investment that is not always available off the shelf, due to production and other constraints. It is therefore paramount that the hose team takes a holistic approach, considering factors such as environmental influence, purpose, design, inventory management, storage and more.
Outsourcing hose management to the right partner can mean updated knowledge and experience of all terminal types, business models and operating environments.
Ideally the hose inventory management and storage program should provide a comprehensive life cycle management service for both subsea and floating marine hoses used in oil and gas offshore terminal loading and unloading facilities. The hose inventory management solution should be based on OCIMF specialist testing guidelines and customised to suit the terminal at hand.
Here a specialist hose partner also holds the upper hand as they will strictly conform to the latest OCIMF guidelines and should be endorsed by their marine hose manufacturing alliance partners.
Hose Storage Services should include the following onshore elements
- Procurement and Supply
- Storage Facilities & Services
- Onshore Hose Maintenance
- OCIMF Testing of stored hoses
- Realtime Tracking
- Hose movement through its entire Life Cycle
- Transportation including Handling, Lifting, and Sea Fastening
- Environmentally Safe Hose Disposal
- Performance Monitoring
At MARSOL we have proven that such a comprehensive hose support plan can optimise the quality and stock levels of spare hoses provided either from in-house stock or Marsol regional Service Centres. It also prevents the use of hoses that are beyond set timeframes or identified as not-fit-for-purpose. We aim to avoid premature hose disposal with proper handling, storage and management practices, so as to maximise the hose lifespan and save overall client OpEx.
With vast experience and knowledge of hose behaviour it is possible for an external hose maintenance partner to improve hose reliability, asset integrity and facility availability by minimising operational and production interruptions associated with hose failure or malpractice. This also allows the hose partner to perform asset tracking which leads to historical performance data gathering for the improvement of predictive life models.
Hose Change Out
Hose Change out solution is an essential component of a comprehensive Hose Life Cycle initiative. The procedure constitutes a significant activity requiring specialised and experienced personnel, combined with proven methodologies to ensure a safe, efficient and cost-effective hose change out. This engineered solution should be custom-designed by the outsourced hose maintenance partner to cater for each client and their specific location, with the endorsement of the hose manufacturing OEMs and Alliance Partners.
Hose Change outs need to be planned in line with OEM recommendations and OCIMF Guidelines.
Submarine and Floating Marine Hose Change out may include:
•Flushing
•Removal
•Towing
•Disassembly or assembly of strings
•Launch or recovery
•Installation
•In Situ Testing
OCIMF testing
Destructive testing
Our objective is to provide a comprehensive, QHSE-Driven, Hose Change out service customised by MARSOL to optimise a client’s available assets and resources. The service allows the client to focus on their core business activities, without the need for additional investment or specialist in-house capability.
Your hose maintenance partner will aim to reduce QHSE risks during change outs through the use of proven methodologies, qualified and experienced personnel, appropriate vessels and assets to ensure the personnel’s safety, environmental and facility protection.
As an outsourced hose maintenance partner is held responsible for damage to infrastructure and assets during installation or removal, you can trust that extra care will be taken to reduce the potential of such damage.
At MARSOL we aim to preserve our client’s corporate reputation and stakeholders’ interests. Choose a hose management partner you can trust.
SPM hose emergency support
Oil & Gas marine hoses are the primary conduits for offshore product transfer. These critical components constitute a substantial investment, often with long lead times, and are the most vulnerable link in the distribution chain. Oil & Gas marine hoses are exposed to harsh environmental and operating conditions, operating to high levels of availability, yet must comply with exacting QHSE standards.
Oil leaks, reduced reliability, reduced asset Integrity and unplanned shutdowns, constitute significant QHSE, reputation and economic impacts for the asset owner, all other stakeholders and the environment. For this reason it is paramount that your outsourced hose maintenance partner has a good emergency support plan in place.
Conclusion
While an in-house team has benefits, a specialist hose management partner can be the better choice. MARSOL provides a comprehensive Hose Management Service which ensures a safe, reliable and fit for purpose operation of marine hoses. The service allows the client to focus on their core business activities without the need for a specialist in-house capability.
Case study: Submarine and Floating Hose Change out
In 2018 Marsol was contracted to undertake the complete change out of subsea and floating hoses originally installed by an EPC contractor 6 years previously. On this particular system, hose sections had never previously been tested individually.
The Problem: Complete Hose Change out
The client’s SPM floating and subsea hoses were reaching the end of their predicted life expectancy and needed to be replaced. In order to minimize disruption to operations, this process had to be undertaken as quickly and efficiently as possible.
Some risks that had to be considered:
- Damaging the new hoses during handling and deployment
- Towing the floating hose and crossing shipping lanes
- Inadequate string assembly if performed at sea
The removal of old- and installation of new hoses on the buoy had to be undertaken as quickly as possible. Removed hoses needed to be inspected and tested to investigate any root causes of failure/wear that may contribute to increased long-term operational costs, and to determine their suitability for reuse
The Solution
Assemble the Marsol Hose Deployment Roller System at a suitable access site on the beach nearest the SPM. Load out hose sections and connect into a string in the dry. Tow the hose off the beach for a straight swap at the buoy offshore. Bring the old hose back to the beach for immediate recovery & disassembly.
The Process
This two-month project was tactically programmed to ensure the minimum viable product for the client, whereby large costs incurred by vessels and dive teams were only incurred for just over two weeks. The balance of the activities were executed by teams “on the beach” who made the materials ready for the offshore works.
To ensure that the SPM system was free from hydrocarbon product, and to avoid any spillage during the hose disconnection, the system was flushed with freshwater that was pumped from the floating hose end through the SPM, subsea hose and into the pipeline. This water-flush pushed the product down the fluid path into the pipeline towards the onshore storage tanks.
Subsea Hoses Change out
In this case, there was only one complete spare subsea hose-string, therefore a set of new subsea hoses had been purchased and delivered to the client ahead of the commencement of the project.
All subsea hoses were loaded on the Multicat Vessel in port, along with the tools and equipment required for the offshore works.
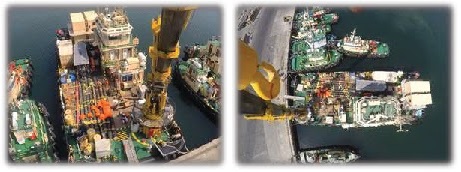
The subsea hose change out was performed on the Multicat deck successfully.
The hydraulic control umbilical was removed by the divers in order to allow work on the subsea hoses without damaging said umbilical. The first hose was then disconnected, removed, dismantled and discharged to a service vessel. The new hose was assembled and deployed into the water and installed under the buoy by the diving team.
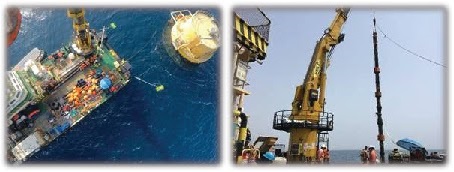
Similarly, the opposing hose was removed and replaced with the new string.
The removed hoses were sent ashore to be tested for residual life and serviceability.
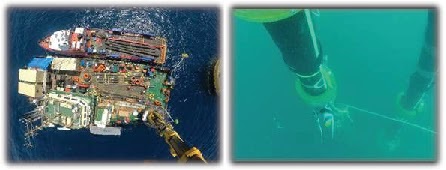
Floating Hose Change out
The second phase of this project was the floating hose change out which, although similar, required a different approach to that of the subsea hose change out.
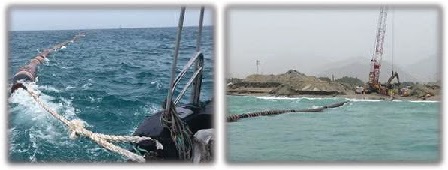
The Marsol onshore team commenced by loading and assembling the new floating hose on the Marsol Roller System. This modular hose deployment system increases efficiency but reduces risks and prevents the hose damage – usually incurred by ground contact and handling. The new Marine Breakaway Coupling (MBC) was assembled in the string and secured with special brackets to avoid activation while the hose string was towed to the SPM.
At the same time, the offshore team disconnected the old floating hose string and stored it, prior to removing it from the water – through the surf zone.
Back onshore, the newly assembled floating hose string was leak tested while on the Marsol Roller System, to ensure the integrity of the flange connections. The leak test was witnessed and signed-off by Class.
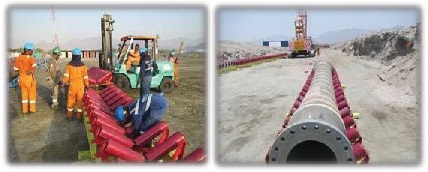
The newly assembled hose-string was then launched from the beach, towed to site and installed on the SPM.
Thereafter, the old floating hose was towed from the storage and recovered using the Marsol Roller System. The removed string was dismantled into individual hoses at the site and made ready for OCIMF testing.
SPM Pressure Test
To conclude the offshore works, a complete SPM system pressure test was performed by pumping water into the system from the floating hose, raising the pressure to the required level and holding the pressure for a certain number of hours. This test was undertaken in accordance with OCIMF and OEM guidelines, and was witnessed by CLASS.
OCIMF Testing and Storage of Removed Hoses
Following the recovery, all old hoses were cleaned, OCIMF tested and those suitable for reuse were stored in the storage containers.
Visual Testing
The result of the OCIMF and OEM visual inspection showed that some of the floating hoses failed the test and had to be retired.
The visual inspection also revealed that some of the subsea hoses had various superficial cuts and small areas of damage on the outer layer, however, those were allowed for further testing to ascertain suitability to be repaired and then held as spares.
Examples of superficially damaged hoses:
OCIMF Test Results
A number of hoses passed with reservations, while the recommendation for others was to be retired and not placed in storage for re-use
Test Result Findings
Based on the OCIMF testing, it was found that the hoses that passed the test could be kept as emergency spares up to the end of their shelf life (Estimated 10 years from the original date of manufacturing, as recommended by OEM and OCIMF guidelines).
Case Study Recommendations
It was Marsol’s recommendation that the client purchases additional spare hoses such that they can respond with replacement parts in case of a failure of any of the hose, or to change out short lifespan hoses like the FOB or Tanker Rail.
The recommendation was that the next OCIMF testing of the spare hoses to be done after two years to ensure that the emergency spare hoses are still suitable for service.
In this case it is planned to perform the hydrostatic burst test which would provide data that could be used to establish suitability for purpose, to gauge the extent of any damage and provide useful information to determine the service life and life extension of the hoses.
This information will be very important for new hose procurement planning.
In Closing
A SPM hose change out may be a routine procedure but is often overlooked as something that is not fully understood but done anyway ‘because it is required.’ This is a dangerous approach in the offshore industry because many protocols and procedures are no longer relevant, efficient or considered best practice. The method that Marsol describes in this article is the result of careful consideration of the particular site, the various design parameters of the assets and real-world conditions. The operation was executed safely and efficiently while exceeding the client expectations.
Let us help you achieve the same result. Get in touch to take charge of your next hose change out.
Project Report: OCIMF testing and Hose change out – what you see is not what you get.
When planning for SPM hose changeout project, it is paramount that the old hoses are tested, as this helps to determine wear patterns and root causes of hose decay or failure. Visual inspection does not tell all about the hoses’ condition and full OCIMF testing is recommended to properly understand the hose condition. Here’s what to expect when you are planning a hose changeout with OCIMF testing project.
Hose manufacturers typically recommend SPM hose changeout after 5 years (depending on certain parameters), but it may also be needed earlier due to unusual wear, damage or failure. Note that certain high-wear hoses have shorter lifespans. Catering for such events becomes easier when you have a solid SPM Hose Plan that favours longevity and sustainable reliability.
When it comes to SPM Hose testing, Marsol follows the regulations brought forth by the Oil Companies International Marine Forum (OCIMF), to ensure safe and environmentally friendly processes that are in accordance with the most modern standardised methods available.
Hose Changeout and Testing Activities and Schedule
First the team will divide the project into phases, depending on the scope. During a complete hose changeout project, the phases are likely to include:
• Phase 1: Testing of the new hoses (if they have been in prolonged storage or used before)
• Phase 2: Replacement of all hoses (Floating and Submarine)
• Phase 3: Testing of the removed hoses
The personnel involved in the phases would follow method statements specifically developed for the asset and its environmental conditions.
At Marsol these method statements are developed in line with the OCIMF Guidelines, International Standards (ISO, ISSGOT), OEM Manuals and industry best practice.
Hose Changeout Timeline
From start to finish, a project changing out a set of floating and subsea hoses can take 4 weeks. At Marsol, the proprietary Roller System for floating hose deployment is used. This system is specially designed to not only increase efficiency, but also minimise hose damage throughout the onshore part of the hose changeout procedure.
Using this system, the floating hose changeout part of two strings will see the SPM downtime reduced to just about a week, given streamlined conditions and excluding any unexpected events.
The team will begin with Mobilisation and Site Setup, to start OCIMF testing of spare hoses as soon as possible. Concurrently, assembly of the Roller System will start, and at the same time, offshore works at the SPM will begin in by disconnecting the old floating hoses and towing them to shore.
The submarine hose changeout and new floating hose installation will be performed next, ensuring that all SPM pressure tests are completed and Class witnessed.
Finally, the old hoses are OCIMF tested to identify potential decay trends or wear patterns that could result in a shortened lifespan. This will also identify hoses that can be reused as spares for times of emergency.
Hose Changeout General Considerations
- Hose testing should be performed according to the OCIMF Guidelines for the Handling, Storage, Inspection and Testing of Hoses on shore, 2nd Edition, 1995
- Both the submarine and floating hoses are to be tested according to the OEM specifications.
- Spare hoses to be used in the changeout should undergo testing according to OCIMF Guidelines before assembly and installation.
This includes:
- Visual inspection
- Hydrostatic pressure test
- Vacuum test
- Electrical test
- All the ancillary materials (gaskets, nuts and bolts) to be used as part of the assembly, will have to be checked.
New SPM hoses that have been factory tested prior to installation do not need to be tested again, as long as the manufacturer has supplied you with testing certificates.
OCIMF Test Data Measuring and Recording
For long-term improvements in operational efficiency, it is important to record data obtained from your hose changeout and testing. This means that every hose tested must be documented, including a visual reference, pressure, vacuum tests and graphs combined with time and pressures.
Indicators of Concern during Hose Inspection
During inspection and OCIMF testing the following indicators should alert the inspector that the hose may be in an unsatisfactory state:
Visual Inspection:
• Excessive cover/floatation damage.
• Crushed or kinked hose wall.
• Local reduction in bore diameter
• Distinct circumferential “ribbing” (indicating fatigue or fabrication flaw).
• Mechanically damaged lining.
• Lining separation from rest of hose wall (delamination).
• Movement of end fitting nipple relative to flexible hose section.
• Bulges/blisters (other than air pockets or local delamination in cover).
• Excessive fitting corrosion.
• Excessive wear to lifting lugs.
Hydrostatic test
• External leakage
• External bulge / bursting appears
• Difficulty holding pressure if not due to equipment malfunction (suggests leak path into hose wall)
In-Situ Pressure test:
• Failure of holding pressure
• Twist Warning System (TWS) activation
• Leak detector activation
Conclusion
SPM hose changeouts, whether they are routine or an emergency, cause down time and loss of operational capacity which is of major concern to SPM operators. It is the aim of every operator to undertake the changeouts as quickly and efficiently as possible. Marsol has developed methodology and the Roller System for hose deployment which ensure maximum speed and efficiency of the changeout process. OCIMF testing of the old hoses after the changeout is critical to understanding the condition of the hoses and any causes of the reduction in their life expectancy. This information can be used to make operational decisions and ensure the root causes of the failures are addressed.
Disrupt the Status Quo with a Holistic Hose Management Partner
The current market needs cooperation and support for EMEA and On Site Assistance, so much so that clients have expressed a market urgency in the hose planning sphere. Currently clients are approaching the market directly or via their agents for assistance. This creates a gap of knowledge transfer where clients have top-of-the-range products, but are unsure how to maintain and operate this optimally.
Market Need for Holistic Hose Planning
When it comes to hose planning, emergency support for immediate onsite engineering in case of failure is the first pain point that comes to mind, but when one approaches hose planning holistically, the market need becomes even more complex.
To avoid numerous emergency scenarios, there is a need for better hose logistics and storage, installation, testing and disposal tools and procedures. Procedures that favour hose life extension while maintaining the low level of risks and high level of performance.
For this reason, Marsol developed its Advanced Systems Integrity Management (ASIM) Program, an all-encompassing solution that ensures quality and efficiency fit for purpose.
Market Development Strategy & Brand Enhancement for Hose Planning
To approach this market need, short term and long term hose planning is required.
Short term services aim to increase volumes per customer.
How?
- Direct sales through Agents
- Provide enhancement services
- Tendering -Upsell Options
- Build relationships through long term call out services
Long term services aim to increase market share without necessity to increase individual clients’ volumes.
How?
- Retain existing clients
- Develop new clients
- Strengthen your brand locally and worldwide
- Through: Differentiators
- Localized rapid engineering response
- ASIM –Integrity management support leading to
- Hose life extension and life cycle management programs
Through short and long term hose planning, we enhance agents capability by supporting agents with value added tools.
This holistic hose planning approach changes focus from basic factory sales into enhanced turn key solution packages including:
•Site assessment (Operational)
•Site Specific Modeling
•Engineering
•Storage
•Installation
•Maintenance
By proactively working with a holistic hose planning service provider like Marsol, agents can offer their clients aftersales and integrity services endorsed by the factory : An approach that disrupts the status quo.
Choosing your Hose Planning Partner
Ensure that your hose planning partner’s people are trained at the factory to ensure OEM aligned solutions and warranty protection programs.
Our Main Drivers
- We reduce client’ costs whilst
- Enhancing the service by
- redirecting expenditure
In order to:
- Maintain the intrinsic value of the facility
- Avoid interruption
- Safe operating practices with reduced risk
- Protect the environment
- Establish possible points of failure and mitigations programs
- Ensuring term cost effective functionality of the facility and assets Contributing to
- Long Term Market Development Strategy & Client Support
Establishing your hose management service focus
Services should address potential points of failure in support of its long term techno-commercial integrity management programs. This includes
- Integrity management and life extension of the facility and its individual components (pipeline, SPM, PLEM, hoses)
- Life prediction of the asset based on design criteria, Cause & Effect studies, and actual site conditions
- Collection and Analysis of the data to achieve realistic prediction and comparison risks
- Spares optimisation, storage, preservation program, cost reduction, material recycling
- Establishing service centers, identifying common denominators thus achieving standardisation and commonality of design
- Achieving economies of scale and optimisation of holding/hidden costs
Such a holistic hose management partnership offers the unique opportunity to combine strengths of both the integrity management partner and the agent supplier’s product specific knowledge and field experience.
Packaging this approach means combining expertise to fulfill the client’s expectations without losing focus on respective core competencies.
Your hose management plan should also be designed to offer
- Optimal risk management
- Minimization of OPEX and downtime costs
- Increased reliability and achievement of max life
- Optimization of CAPEX and OPEX Expenditure while considering cause and effect.
Best Practices for your SPM Hose Management Plan
Are you putting together your SPM hose plan or revisiting your O&M strategy? Here we discuss examples of marine hose applications, lessons learned and best practices that help you to fulfil your fiduciary duties.
GREENFIELD OR BROWNFIELD SPM Hose plan
It’s never too early or too late to start your SPM Hose plan the right way.
When hoses begin to show symptoms or points of failure we apply the following process:
1. Find Root Cause
Before you hastily begin to treat symptoms such as ruptures, for example, ask yourself why they have occurred in the first place. This will help you identify numerous holistic factors that could be affecting your SPM hose plan.
2. Assumptions vs Facts / Data / History
Don’t let years of experience blind you. No two terminals are exactly the same.
Change is a constant and the sooner you realise this, the sooner you will begin to value data that can guide your SPM hose plan.
3. Analysis / Knowledge + Experience
Once you have obtained the required data, you can begin to cast an analytical eye.
This is where the application of knowledge and experience is pertinent. Derive correlation and explore all known and unknown paths.
4. Proactive Long Term Solutions
When you have successfully identified the root cause and you have taken into account all holistic factors, you can begin to create a more robust SPM hose plan with long term durability, efficiency and sustainability in mind.

Determining the root cause of issues in your SPM Hose Plan
When looking for symptoms of failure in your SPM hose plan, it is paramount that you determine the root cause through holistic analysis.
Here are some pinpoints to look for.
List of Hose Indicator examples
- Wrap-around
- Kinking
- Auto-submergence
- Change in buoyancy
- Contact
- Sheltering & Chafing
- Leak detector activation
- Catastrophic Failures
- Bearing
- Hose Handling
- Contact
- Float Loss
- String Length
- Environment
- Handling
- Exceeding hose life

SPM Hose Plan – Lessons Learned
In this section, we highlight two case studies, each with its own challenges and bespoke solution for the best performing SPM hose plan.
Case study 1: Changing Environment
In this project, our belief that change is constant was yet again proved by the ever-changing environment and its effects on terminal efficiency and longevity.
Project overview
- System Design
- Assumptions
- Regional data vs Site-specific data
- Landscape changes
- Coastline changes
- Operational consequences
What the hoses told us:
Upon inspection of the current hoses in use, we discovered that local conditions have changed from the basis of design. This was clear through the hose misbehaviour and symptoms, or points of failure.
Symptoms:
Rapid abnormal wear of floating hoses and tanker rail components.
Our listening method:
Collected and analysed data
What we heard:
Through SPM hose plan analysis and site experience we identified
- Root Cause
- Cost-Effective Solutions
- Optimum hose life

Case study 2: Design Assumptions
In this project, we investigated the effect that seabed assumptions in modelling can have on hoses, buoys and PLEM loading.
Project overview
- Seabed variations
- Winter and summer positions
- Near and Far Scenarios
- Understanding current direction & magnitude throughout the water column
- Effect on behaviour and integrity
What the hoses told us:
These hoses showed signs of impact that not only required a temporary fix to preserve the current hoses but also long term solutions that would prevent further damage.
Symptoms:
• Subsea hose string to hose string contact
• Subsea hose string to seabed contact
Our listening method:
Collected and analysed data
What we heard:
Through SPM hose plan analysis and site experience we identified
• Chain trenching, affecting chain pretension
• Increased buoy excursion
• Predominant winter & summer buoy position
• Change in hose profile

Fiduciary duties linked to your SPM hose plan
It is your fiduciary duty to make informed decisions regarding your SPM hose plan.
If you listen to your system you will get to know it. Once you know your system intimately any changes in performance or signs of upcoming symptoms will easily be noticed. This will help you adapt to change and maintain the intrinsic value of the facility.
It is your fiduciary duty to avoid interruption in your efficiency by predicting system behaviour. This, in turn, will help you to protect the environment and offer safe operating practices with reduced risk.
When your system is understood holistically you will begin to progress from O&M towards integrity, resulting in all the above-mentioned successes.
Conclusion
It is important to give SPM Hose plan management the tools to make informed decisions regarding hose and system O&M.
At Marsol we strive to share our holistic philosophies that have proven success time and time again.
- Listen to the hoses
- Find the root causes
- Implement optimum solution
These best practices within the SPM hose plan enable design modifications and operational changes that are fit for purpose.
Is your management team equipped with the best tools and processes for the job? Find out today.